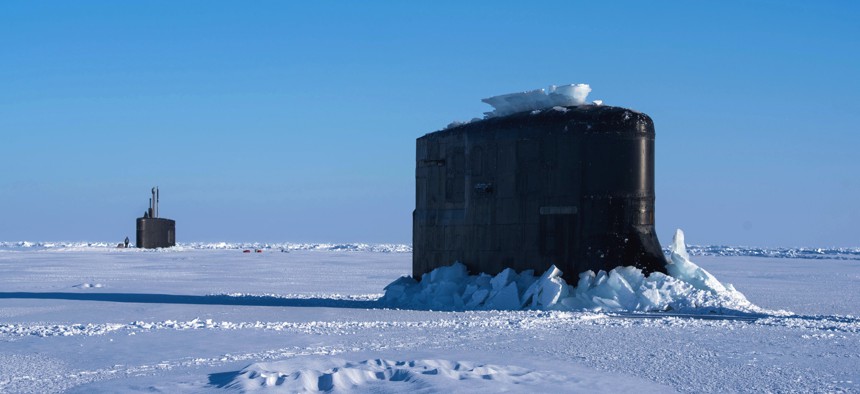
The Seawolf-class fast-attack submarine USS Connecticut (SSN 22) and the Los Angeles-class fast-attack submarine USS Hartford (SSN 768) break through the ice in support of Ice Exercise (ICEX) 2018. U.S. Navy / Mass Communication 2nd Class Micheal H. Lee
How Digital Twinning Is Helping Improve Submarine Communications
Lessons from the challenging world of undersea operations ought to be applied across the military.
One thing slowing down the upgrade cycles of weapons is the painstaking effort it takes to predict the reliability, maintainability, and availability, or RMA, of modernized parts or systems. However, the U.S. Navy’s submarine communications managers have found a way to slash months off the process of “RMA vetting”—that is, tests and other efforts to anticipate problems. Other military programs should take heed so they can upgrade performance or replace obsolete parts as quickly as possible.
The secret is digital twin modeling. A one-time investment to set up a digital twin enables comprehensive RMA analysis for each modernization cycle without the time and cost of field-testing equipment.
It’s important to understand why traditional RMA vetting is so difficult. Field-testing opportunities are limited because submarine communications systems are too important to risk deploying unproven test units. It is also costly, if not entirely impractical, to create physical test versions that mirror the real-world conditions of ocean and warfare.
In the absence of practical tests, RMA analysis is performed by teams of experts who estimate performance for each mechanical, electro-mechanical, software and communications interface. This task is difficult under normal circumstances. It is further complicated by the lack of centralized fleet-wide failure data that could inform estimates for upgraded parts or subsystems. These experts spend most of their time tracking down historical failure data from a hodgepodge of sources, and then roll up and apply those estimates to assess RMA for the complete system. This painstaking process takes weeks, even months.
The approach the Navy submarine communications community is using to speed up modernization of its systems boils down to three key components.
First, create a digital twin. This means digitally replicating a baseline model of the system, including all components, connections, and functionality. The twin models every operational thread performed by the warfighting system, mirroring how those threads move through each component. The model’s component-level RMA data helps analysts predict system reliability at various levels, from simply turning things on all the way up to performing real-world missions.
Second, populate the model with real-world historical reliability data from across the fleet—including when, where, and how systems failed. This will become even more powerful as the Navy rolls out procedures for systematically capturing and storing failure data to give analysts an authoritative source for identifying trends across the fleet.
Third, use simulations to test the warfare platform’s key operational threads. The fully functional digital twin, populated with accurate RMA data, helps system planners quickly review different modernization alternatives, thereby avoiding the manual analysis that previously took weeks or months. They can confidently predict which approach will best keep the modernized system ready to fight.
The result of the Navy’s approach to systems modernization is weapons that can add functionality or replace obsolete components quickly. Maintenance schedules also can be optimized for deployed systems by predicting when mission-critical elements will need service or are likely to break. Other military programs should consider this approach in modernizations of their own weapons and systems.
Tracy Gregorio is CEO of G2 Ops, a woman-owned cybersecurity and IT engineering services company serving government and commercial enterprises.
NEXT STORY: The PLA’s People Problem