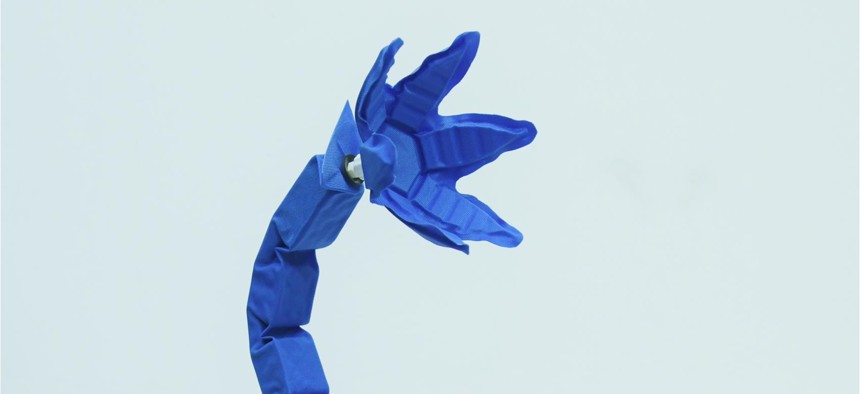
A "soft robot" snake arm designed by Harvard's Wyss Institute and MIT's CSAIL institute HARVARD WYSS / MIT CSAIL
A Breakthrough in Soft Robot Muscles, Funded by the Military
Future military robots may come in softer, more cuddly, and stranger forms.
Back-flipping robots made of metal and other hard materials may be a big hit on YouTube, but future military robots may need appendages that are far softer, stronger and flexible — more like natural muscle tissue.
Funded in part by the Defense Advanced Research Projects Agency, a team of researchers from the MIT Computer Science and Artificial Intelligence Laboratory, or CSAIL, along with scientists from Harvard University’s Wyss Institute, have created robot “muscles” that use hydraulics rather than electric motors. These muscles are strong – the researchers say their 2.6-gram robot muscle can lift a 3-kilogram object, like a “mallard duck lifting a car” — and can shrink to 10 percent of their original size, all while using much less power than typical metal-and-circuit robots.
The new soft robot muscles share a lot with animal muscle tissue. Where humans have muscles, robots have what are called actuators, little mechanisms that control movement. A humanoid robot with lifelike facial expressions, for example, has a bunch of actuators buried beneath the surface of the “skin,” working together to lift the bot’s eyebrows, the corners of the mouth, etc.
Most robotic actuators are electric and run on battery power — a lot of it . It’s one reason why many robots (and robotic exoskeletons that also use electric actuators) are somewhat impractical in many military settings. Who wants to carry multiple lithium-ion battery packs with them to power their exoskeleton behind enemy lines?
The Wyss-CSAIL robo-muscles work via hydraulic actuators, using water and air. They consist of a carefully designed “skeleton” of metal or some other material folded into a vacuum-sealed bag. As air or water is added or removed from the bag, the change in pressure causes the skeleton and the skin to fold or unfold in a way that allows for gripping, pushing, or other limited functions.
“One of the key aspects of these muscles is that they’re programmable, in the sense that designing how the skeleton folds defines how the whole structure moves. You essentially get that motion for free, without the need for a control system,” Shuguang Li, a researcher at Wyss Institute and CSAIL, said in a statement.
Moving away from electric actuators toward more organic ones can also make robots easier to run, reducing the amount of computer processing needed to get the robot to perform as intended, say the researchers. “Incorporating intelligence into the body (via specific folding patterns, in the case of our actuators) has the potential to simplify the algorithms needed to direct the robot to achieve its goal. All these actuators have the same simple on/off switch, which their bodies then translate into a broad range of motions,” said MIT researcher Daniela Rus.
Lightweight, high-power muscles also broaden the range of applications for robots, everything from soft exoskeletons for carrying heavy loads longer distances to, potentially, small robots that can be ingested or implanted in the body to perform specific biological tasks. The researchers have shown that they can build the robo-muscles with a water-soluble polymer that dissolves when no longer necessary (so it doesn’t stick around inside longer than it needs to). And they can be scaled to almost any size.
Their paper (here’s a draft version ) will appear in the Proceedings of the National Academies of Sciences this week.