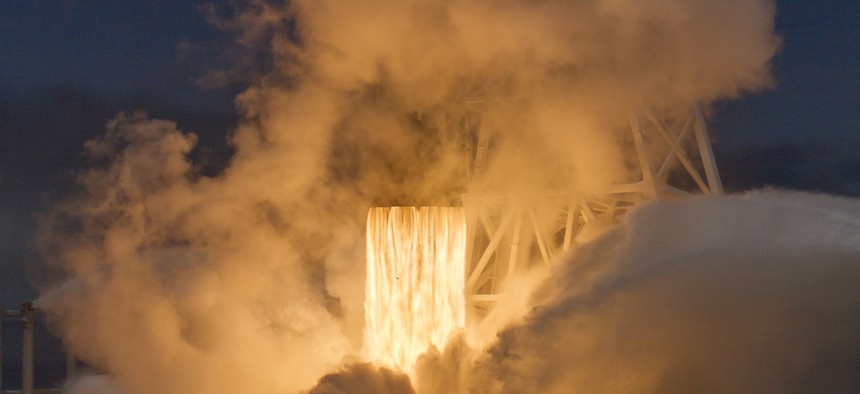
In this photo provided by NASA, a SpaceX Falcon 9 rocket with a pair of U.S.-German science satellites and five commercial communications satellites takes off from Space Launch Complex 4E at Vandenberg Air Force Base in California on May 22, 2018. Bill Ingalls/NASA via AP
How Rocket-Makers Ensure 3D-Printed Parts are Strong Enough for Space
Measure them against an industrial standard for welding called AWS D17.1 Class A.
Some people are skeptical about 3D printing machines like rockets. Their view is that hardware made by precisely spraying hot metal into shape can’t possibly be as strong as hardware assembled using fusion welding.
Still, cost-efficiency means most aerospace companies do make use of additive manufacturing in their supply chain. Relativity Space, a Los Angeles start-up, makes more use than most, and has promised to build almost an entire rocket with a large, custom-made 3D printer.
Relativity Space CEO Tim Ellis says his printer has passed an industrial standard for welding called AWS D17.1 Class A, which has stringent rules for quality. ”That’s the standard you would use for fracture-critical, mission critical parts that cannot fail,” he says. Ellis gave Quartz a rare look inside the process.
So how do you know if your 3D-printed part is strong enough? By checking your work with powerful X-Rays and a microscope. At first, you might see results like these, which are from metal parts that Relativity printed two years ago while still developing its technology. An X-Ray scan shows irregular formation and jagged edges:
Then, the microscope reveals microscopic cracks in the surface of the hardware:
Today, Relativity’s printer is producing far different results. X-Ray scans show a uniform part with clean edges:
And the microscope shows no tiny fractures or pores in the surface of the metal:
The stress of sending a rocket into space faster than the speed of sound is extreme, and even the tiniest flaws can lead to a disastrous failure. Getting the vehicle right means sweating the details—down to 500 micrometers.