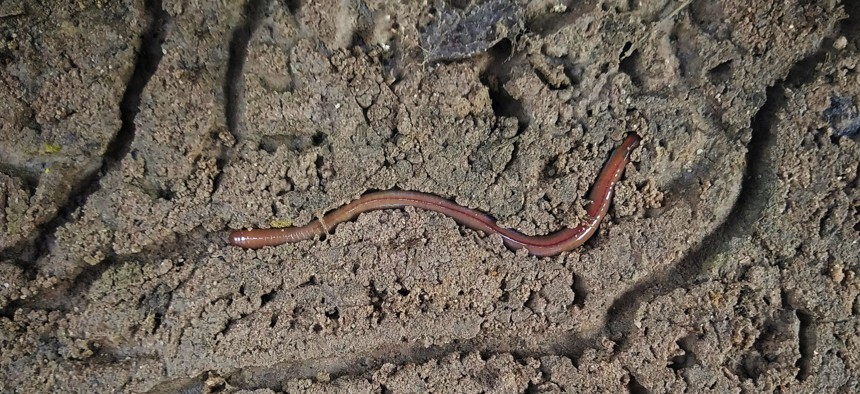
Golf Bress / Shutterstock
DARPA Funds Earthworm-Inspired Soft Robot to Dig Tunnels
As part of the Underminer program, General Electric’s innovation arm is perfecting a soft robot to boost battlefield operations.
General Electric Company’s technological development division GE Research is creating and refining a soft and smart tunnel-digging robot—inspired by the makeup and movements of earthworms—that could underpin critical underground military operations of the future.
The research wing was recently tapped for a 15-month, $2.5 million project through the Defense Advanced Research Projects Agency’s Underminer program to perfect and prove the capabilities of its already-designed robotic prototype, which insiders believe will also have applications beyond the battlefield.
“The key objectives of the DARPA program are to demonstrate a robot that can move at a speed of 10 cm/sec and dig a tunnel that is 500 meters in length and at least 10 cm in diameter,” GE Research’s project leader Deepak Trivedi recently told Nextgov. “We have made great progress in the project thus far and are on track to meeting these objectives.”
Through Underminer, DARPA aims to explore and demonstrate the rapid construction and uses of tactical underground tunnel networks to support the U.S. military’s efforts amid harsh environments. The ideal end result would be new solutions incorporating advanced robotics and sensing technologies that can outperform present commercial drilling capabilities. Aside from GE, the agency also selected teams from Colorado School of Mines and Sandia National Laboratories to demonstrate their own tech solutions and integrations.
Related: Border Patrol Wants Robots that Can Go Underground and Report Back
“The ability to quickly bore tactical tunnels could benefit contingency operations such as rapid ammunition resupply, rescue missions, or other immediate needs,” DARPA’s program manager Andrew Nuss told Nextgov Tuesday. “As a research and development agency, DARPA's role is to advance technologies to address national security challenges.”
He added that the agency’s transition partners in the military services would ultimately determine the timelines for precisely when these new in-the-works solutions might be deployed to support operations on—or under—the frontlines.
The inspiration for GE Research’s earthworm-mimicking soft robot and overall approach to the ongoing project stems from Trivedi’s graduate and doctoral research during his time in Penn State University’s mechanical engineering program. Embarking on his doctoral work—which GE’s release notes was “one of the earliest in soft robotics”—Trivedi sought to build and demonstrate a biologically-inspired robot based off of naturally occurring soft structures, such as the arms of octopi or the trunks of elephants.
The earthworm-like robot now being produced for DARPA incorporates some of his previously developed characteristics like squeezing through tight spaces, while also being equipped to dig deep and rapidly move around. So far, GE’s team designed a prototype that is multiple feet in length, with artificial muscles that deliberately imitate earthworms’ agile movements through soil and, according to GE’s release, it traverses “with the force of tree roots penetrating through soft rock.”
Though the team didn’t work with live earthworms in the effort, Trivedi said much of their understanding and insights were formed reviewing scientific literature, “which provided rich detail on how earthworms are able to move so efficiently through soil and can carve out nearly perfect tunnels.”
“It’s how they move that intrigued us most,” he said.
Earthworms rely on a flexible-but-powerful muscular structure filled with fluid, called the “hydrostatic skeleton,” the mechanical engineer explained—and that structure poses a stark contrast to conventional robots, which have rigid structures and discrete joints, limiting their ability to operate in unstructured and congested settings. Trivedi and team’s robot is made up of powerful, yet soft, earthworm-imitating “muscles” that he said enable it to “function in a similar fashion to a real earthworm in nature.” This system will adapt and autonomously change its gait in response to shifting soil conditions and eventually have a range of more degrees of freedom in movement that traditional bots with joints.
“The robot can apply large forces for making the tunnel, yet easily steer through obstacles due to its flexible structure,” Trivedi said.
In their effort, the research team is taking a “very agile and iterative approach,” quickly fabricating new designs of robot-related prototypes as they uncover new insights from their tests and experiments. And one of the shifts they’re set on making early on is a move from a pneumatic to hydraulic muscle system for powering the movements of the robot. Initial prototypes for the project use a pneumatic system, which Trivedi explained relies on compressed or pressured air.
“Hydraulic systems rely on liquids, which is more consistent with the makeup of earthworms,” he noted. “Earthworms use a combination of liquid and muscles to move efficiently through the soil.”
The work is cutting-edge and soft robots are not yet the mainstream, so what Trivedi called the “building blocks” behind them—components like soft sensors and actuators—usually do not exist commercially. This means “a lot of ingenuity and effort goes into designing and fabricating reliable and capable soft active components for these robots,” he said, noting that while this might be a challenge, it is “also an opportunity for advancing the state of the art.”
The team already performed some initial lab scale demonstrations of the robot tunneling through dirt, as well as some outdoor testing of the prototype. On top of perfecting the emerging robot’s structure, another top priority going forward is to “build more autonomy” into how the smart structure moves and operates.
“In the future, we’d like the robot to be given a destination from point A to point B that it can seek and find on its own,” Trivedi said. “This will require the integration of artificial intelligence, sensing controls and automation technology.”
To that end, the team plans to tap into AI and sensing expertise from insiders across GE’s Research Lab. And though DARPA’s end use for the to-be-completed solutions are being created with the intent to support U.S. military personnel, Trivedi said the use of the tool is not solely limited to underground tunneling. The company already previously produced and field-tested snake-like robots that could be used for jet engine inspection and repair.
“The work DARPA is funding also could lead to other significant advances in soft robotics that open up a whole new set of applications in new areas like industrial inspection and infrastructure such as optical fiber for high speed internet in remote places,” Trivedi said. “So much of what DARPA funds has a positive multiplier effect when it comes to technology advancements and paving the way to new applications, and this program could have similar positive impacts down the line.”